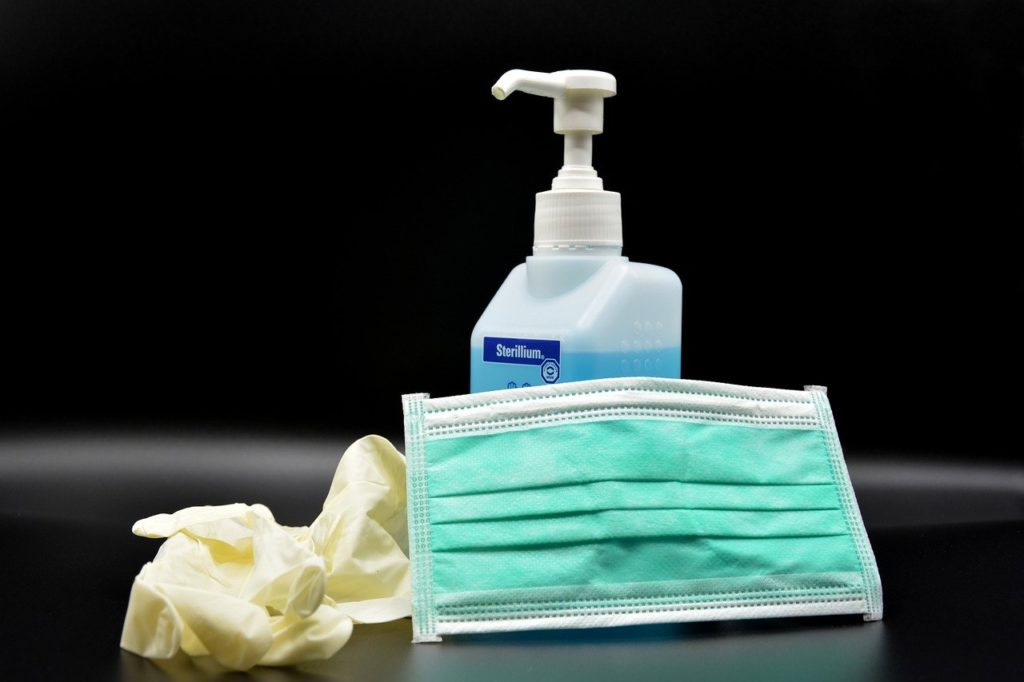
Top Tips for Moving from COVID-19 Manufacturing to Permanent – A Quality Perspective
The COVID-19 pandemic has forced companies to change the way they do business and has also encouraged new business growth. Two of the areas where we have seen an increase in new growth has been in the Personal Protective Equipment (PPE) area, particularly face/surgical masks, and in the hand sanitizer area. Each of these areas have seen significant new growth in manufacturing and distribution.
Many of these new businesses or new business functions within established companies will be seeking to move from manufacturing and distribution during the COVID-19 pandemic under the FDA Emergency Use Authorization to a permanent business model. When this happens companies in this position will need to take a few steps to ensure they remain in compliance with FDA requirements.
Regulatory agencies, including the FDA and others, will expect manufacturers to comply with current regulations and guidelines.
Below are a few steps you can take to be prepared for making the switch to a permanent manufacturer and be inspection ready!
- Perform a GMP Gap Analysis: Compare your current organization, personnel, facility, equipment, product control, process controls, warehousing and distribution, records and reports against current FDA and applicable regulatory standards. This type of analysis is called GMP Gap Assessment.
- Analyze your current Quality System: For medical devices such as face masks or respirators your quality system should comply with 21 CFR 820 and ISO13485:2016. For hand sanitizer companies your quality system should comply with ICH Q10 Pharmaceutical Quality System and ICH Q7 Good Manufacturing Practice Guidance for Pharmaceutical Ingredients. This type of analysis is called a Quality Systems Audit.
- Ensure Quality Control testing is in place: For example Hand Sanitizer is considered an Over the Counter (OTC) drug by the FDA and must have full USP testing and Certificate of Analysis as well as long term stability testing in place. Face/Surgical Masks must meet ASTM F2100-19 testing standards.
- Analyze your Supply Chain: FDA regulated manufacturers must ensure their supply chain of equipment, components, raw materials suppliers and vendors are in compliance with FDA regulations and guidelines.
- Ensure your regulatory submissions are completed and products approved. Face/Surgical Mask and Respirators manufacturers may need FDA 510k approval. Hand Sanitizer manufacturers will need drug product approval. Consult with a regulatory consultant to ensure you are in compliance with regulatory requirements.
Quality Audit Consulting is here to help you with your questions, auditing, consulting and Quality System needs. Please contact us we would love to help:
matt@qualityauditconsulting.com